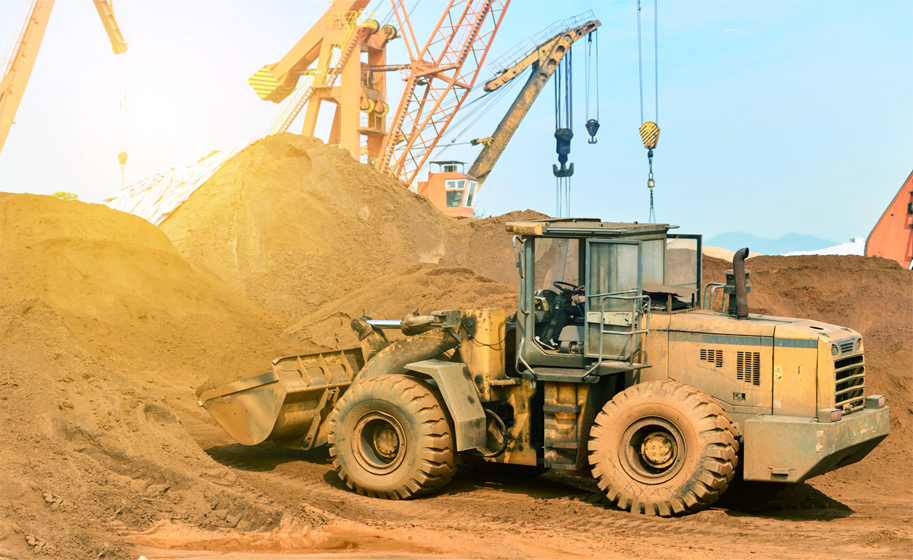
Dealing with Mining Stockpile Challenges
Management of Stockpiles on the Run of Mine (ROM)
Blending material and stockpiles on the ROM need to be managed in a way that ensures safety and stability while also maximising the economic value of the mining operations. This typically requires careful planning and execution, as well as ongoing monitoring and maintenance of the ROM fingers.There are several factors to consider when managing fingers and long-term stockpiles, including the size and shape of the stockpile, the type of material being stockpiled, the equipment being used to reclaim the stockpile, and the surrounding area (Management of tips and Stockpiles. (n.d.) . The approach taken will also depend on the specific site conditions and blending requirements.
It is important to ensure that tips and stockpiles are stable and do not pose a risk to workers or equipment. This may require changes to the way they are operated, such as altering loading methods or providing access ramps. It is also crucial to maintain suitable drainage around the stockpiles, as poor conditions can lead to instability the fingers and the whole ROM pad. In some cases, it may be necessary to reduce the size of a stockpile if it becomes too large or poses a potential risk. This must be done in a controlled manner to avoid any accidents or damage. Overall, effective management of tips and stockpiles on the ROM is essential to ensure safe and efficient operations of the crusher. In many cases, it is critical to allow enough space to access claim the stockpiles as well as wider skyways for dumping operations. The level of risk must be assessed on a case-by-case basis, taking into account all relevant factors. Sufficient precautions must be taken to ensure that risks are minimized and that the stockpile is maintained in a stable condition.
Drill and Blast Performace
Drill and Blast is an essential components of mining operations. It involves the use of drills, mining explosive equipment, mobile mixing units, explosive loading units and use of explosives such as ammonium nitrate emulsion , Ammonium nitrate–fuel oil (ANFO) and explosive primers and booster for breaking up the rock mass. This process is important in making sure the mine is accessible and that the desired ore can be extracted.
The flow of the broken stocks depends on the drill and blast operations at the mine. Efficient and effective drill and blast operations lead to better mining performance, increased productivity, and lower costs.
Management plays a critical role in ensuring that drill and blast activities are carried out at an optimal level ( Information Alignment, 2021). Proper management ensures that broken stocks are removed in a timely manner and that stocks are at an appropriate level to avoid any delay in mining operations. Drill and blast engineers and crew oversee the operations of the drilling equipment and ensure that they are properly utilised. They also keep track of the blasting shots in the pipelines and make sure that they are turned over in proper time. The blasting crew must work closely with production teams, drill and blast engineers to ensure that the blasting operations are carried out at the correct level. Regular maintenance of drilling equipment is also crucial to ensure that they are at optimal performance. In conclusion, drill and blast operations are critical to the success of mining operations and require proper management to maintain efficiency and prevent unnecessary delays.
Impact of low broken stocks on Mine Performance Budgets and Plans
If there is a lack of enough blasted rock in a mine, it can affect the performance budget and plans. This is because the mine needs to provide a planned crusher feed to meet the mine plan target. If there is not enough blasted rock, the mine may not be able to meet its targets. The availability of sufficient stockpiles at a mine site is a critical factor for achieving the production targets set by the management. These stockpiles provide a buffer zone in case of unforeseen disruptions (Ajak et al., 2019), equipment breakdowns, or transportation issues, thereby ensuring that production remains steady. However, when there are not enough blasted stocks available, the mine performance budgets and plans get affected significantly. In such situations, the production team may have to reduce their output or slow down the mining process, which leads to delays in meeting the production target. This, in turn, has a cascading effect on other aspects of the mine, including the costs, revenue, and profitability. Moreover, it can also lead to the wastage of mining resources, including energy, labour, and equipment. Therefore, the mine management must focus on maintaining adequate stocks and ensure that their production team can meet the production targets without any hindrance.
The link between the Mine Geology and ROM Stockpiles
The stability of mine walls and geotechnical issues are critical considerations when dealing with broken stocks. In the mining industry, the management of these issues is essential to avoid costly delays and potential safety hazards. This instability can be caused by numerous factors, including geological structures, excavation methods, and mining-induced stress. To prevent such occurrences, mine management must ensure proper monitoring and analysis of wall conditions and geotechnical risks. This involves regular inspections and assessments of the site, including rock mass identification, rock quality designation, and the identification of potential hazards. Measures such as rock reinforcement and ground support systems may also be implemented to reinforce the walls. By maintaining stability in mine walls and effectively managing geotechnical risks, drill and blast activities can occur smoothly in the mining areas. The mine geology, sampling results and survey affect the delivery of mine stockpiles on the ROM. The factor that affects the most is the ore grade. If the ore grade is high, then less material is required for blending as quality can easily be met given the high-grade material being mined. This in turn allows the mine to haul waste to expose more ore to balance the flow depending on the budgeted strip ratio. If the ore grade is low, then more material must be mined and stockpiled for blending to produce a given quality, and hence the overall cost increases.
Stockpiles material tracking
The Mine Performance Product Tracking (MPPT) system tracks the movement of stockpiles on the run of mine (ROM), from the time the blast shots are blocked out by mine geologists, mined and hauled to the ROM until they are depleted. The system captures data on the location, size and grade of each stockpile, as well as the quantity of material mined from it. This information is used to improve mine planning and operations and to monitor compliance with the mine plan.
Effective tracking of stockpiles in a mine is critical for maintaining good mine performance, and the monitoring of tonnage on the run of the mine is an essential part of it. The management of stockpiles not only ensures that sufficient material is available for processing but also provides a comprehensive understanding of the resource available. This is where Mine Performance Product Tracking comes in, allowing for real-time monitoring of stockpiles so that the right amount can be allocated to meet production requirements. By tracking the tonnage on the run of mine, it is possible to ensure that stockpiles don’t become under or over-utilised, thereby reducing costs and improving the bottom line. In addition, data collected from the tracking system can be analysed to aid in long-term planning for production and resource allocation. Overall, this type of monitoring and tracking is crucial for maintaining optimal mine performance and efficiency.
Integration of Mining Processes
The advances in technology allowed the mining process to be connected and operated as one value chain. This integration depends on the use of Artificial intelligence (AI) in managing mining operations as AI provides several potential benefits. An example of this is the Connected Mine Performance ( Information Alignment, 2021), which is a performance-based mining operation that provides real-time data to equipment and personnel in the field. This information is used to manage and improve the efficiency of the mining process. The Connected Mine uses a variety of sensors and devices to collect data, which is then transmitted to a central unit for analysis.
This data is used to improve the management of the mine, drive operational improvements, and identify potential problems. One of the key aspects of connected mine performance is the ability to drive efficient equipment management by using data analytics to determine the optimal times for maintenance or replacement. The insight from the data is used to improve the management of the mine, drive operational improvements, and identify potential problems before they occur. This can help reduce downtime and improve overall productivity. Another important aspect is the ability to manage drilling and blasting activities with greater precision, which can minimize waste and improve safety. Connected mine performance also involves monitoring every unit of the mine operation, enabling real-time tracking of equipment and personnel. This ensures that safety protocols are being followed and can help identify anomalies or potential issues before they become significant problems. Therefore, integration of the mining processes with the help of modern technologies can significantly improve overall efficiency and safety while maximising yields and reducing costs.
References
Ajak, A. D., Lilford, E., & Topal, E. (2019). Real Option Identification Framework for Mine Operational Decision-Making. Natural Resources Research, 28(2), 409–430. https://doi.org/10.1007/s11053-018-9393-4
Connected mine performance | Mining data collection system. (2021, August 6). Information Alignment Pty Ltd , Mine Data Collection. https://inapl.com/blog/portfolio-item/connected-mine-performance/
Health and Safety Authority.Management of tips and stockpiles. (n.d.). https://www.hsa.ie/eng/your_industry/quarrying/stockpiles_tips_and_lagoons/management_of_tips_and_stockpiles/